Written
by Ed Craig. (170 pages).
This
is the world's most unique robot and manual, self teaching, MIG weld process control
training book. With a few hours reading, this book will show you how to simplify
setting any manual or robot MIG steel or stainless weld.
This is the MIG weld
data you need to consistently attain optimum MIG weld quality and productivity.
For process optimization, this unique book presents Ed's easy to remember Weld
Clock Method and provides the solutions necessary to optimize both manual / robot
weld quality and production efficiency. The robot data optimizes weld production,
eliminates the weld causes of robot down time, and greatly reduces weld defects.
E-mail:
Ed, I purchased your self teaching robot weld process
control training materials a few months ago and I have revised the robot tube
welding parameters with great success. Thanks to you both the weld quality and
production on our automotive exhaust pipes & mufflers were greatly improved.
Best
regards,
D. Juhan
Hundreds
of
companies in twelve different countries, use Ed's self teaching weld process control
training materials. Two of the largest North American robot integrators, Prodomax
and Genisis provided their weld robot engineers and technicians with Ed's unique
MIG process control training resources.
With
billion dollars in annual sales Tenneco, Magna and Dana have found robot weld
success using Ed's materials. When Magna decided it wanted to establish a North
American robot MIG Weld Best Practices and Process Control training program, Magna
assessed what training resources were available in North America and selected
Ed's unique Robot Process Control Work Shop and training books for it's US training.
When
a General Dynamics, USA, Army Ordinance Division, wanted to optimize the manual
MIG weld quality in one of it's major bomb making facilities, they provided their
employees with Ed's Process Control Training Program and resources.
One
simple way to eliminate weld personnel from "playing
around" with the manual or robot welding controls is provide them
with this book, Ed's video and the robot process control training CD program.
In a few hours with these unique training resources and your weld decision makers
will know how to;
[a]
Attain the highest manual weld deposition rates or the fastest robot weld travel
speeds without jeopardizing the weld fusion potential.
[b]
Reduce weld spatter and weld smoke to minuscule levels.
[c]
Eliminate robot weld burn through on thin gage parts and parts with gaps.
[d]
Eliminate robot arc start / arc end problems,
[e] Eliminate contact tip
issues and wire burn backs etc.
[f]
Provide the best weld data and techniques for welding thin gage and thick parts.
[g]
Know when to utilize short circuit, spray or pulsed.
[h]
In a few minutes, optimize manual or robot short circuit, globular, spray or pulsed
parameters.
[i]
Know which wire and gas consumables are most effective on any application, (not
the data provided by salesmen).
[j]
Know how to set an effective "Weld Process Control Program" for either
manual or robot weld productivity and quality consistency.
Ed
set the robot welds for Volvo Cabs, Corvette, Harley and Ford 150 truck frames.
IS
WELD PROCESS EXPERTISE IMPORTANT TO YOUR ORGANIZATION?
COULD YOUR WELD PERSONNEL
ANSWER MIG WELD QUESTIONS LIKE THESE?
Fundamental
Spray Question.
You
will be robot welding 10 to 12 gage carbon steel or stainless parts
using short circuit transfer. The weld size is a 4-5mm fillet. The weld wire is
0.035 (1mm) E70S-3 and the wire feed rate is 280 inch/min. The weld travel rate
is 30 inch/min. You find the weld parameters are too cold, you want to attain
better weld fusion and speed up the robot process. In the robot pendant You decide
to set the "low end" of MIG Spray Transfer weld parameters for the fillet
weld.
[]
What is the optimum "low end wire feed and voltage" setting for
that spray transfer weld with that 0.035 wire?
[]
How will the deposition rate you set for the spray weld, be different from the
short circuit deposition rate and what will those deposition rates be?
[]
As the deposition rates influence the robot weld travel rate, what change
will you make to the robot weld travel rate?
Fundamental
Pulsed Question.
You
are pulsed welding and there is weld spatter on the part. You adjust the "trim
voltage" (arc length), nothing happens.
[]
What other pulsed parameter change will rectify the arc length situation?
Are
you fed up trying to put out the weld fires?
Would you like to leave work at 5 PM
and put those robot weld issues behind you?
Why not have all your weld
personnel, robot programmers, operators, supervisors, engineers designers and
QA personnel, read and answer the 170 process control questions found in this
book. With a few hours of reading, your weld decision makers will become an effective
process control team, a team which for the first time will all walk down the same
process control welding path. A team with the MIG weld process expertise necessary
to provide consistent, optimum weld quality and productivity on any manual or
robot carbon steel / stainless application.
I highly recommend you utilize
this book with my easy to use, robot MIG / MAG Process Control, training CD, along
with the DVD, as listed in the training resource section.


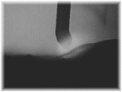
E-mail.
E-mail
Ed.
I am a welding engineer working in the UK. I recently discovered your excellent
web site and process control training resources. I just wanted to drop you a line
to express my thanks for the excellent information.
Yours
Sincerely. Richard Powell.
England.
E-mail
Ed.
I wanted you to know I have just announced that I am leaving my company. I am
going to work for a robot weld integrator. I will be the head of the welding applications
department and will be specifying process, wire, training, techniques, etc. I
am very very excited about this opportunity to learn more about welding and to
help others to see the light. I hope that we can stay in contact as the years
go on. Most importantly, I just want to thank you for the
great information, books and your welding passion that you passed on to me. They
are what got me started in the quest for more real world weld knowledge. In my
new position I will be able to do this full-time and could not ask for a better
position at this point in my career.
Warmest
Regards.
Jeff Winter.
Canada.
E-mail
July 06:
Jan
2007: Ed I wanted to send update about that E-Town plant that you visited a few
years ago: As you know on your first visit to this plant, our robot lines were
producing less than 40 truck frames per-hour and
the majority required extensive weld rework. Thanks to your weld process control
/ best weld practices recommendations the results from our employees are today
staggering. Yesterday this plant hit very close to a record of 76
frames jobs per hour. We daily attain our average goal of one frame per-minute.
We had two recent weld audits. One weld audit had a total of two failures, and
the 2nd weld audit was the first 100% pass weld audit in the history of the F-150
line.
A
Grateful Employee
Dana Corporation.
March
2007: Update from Ryan. Hey Ed:
Just thought I would drop you a line and let
you know that in the beginning of April we will be working on switching over the
5th Dana plant to your process recommendations of an 0.040 wire and the traditional
spray mode instead of the 0.052 wire and Rapid Arc (Lincoln's recommended pulse
MIG program). Thanks again Ryan.

Visit
Ed's MIG and flux cored
Process Control Training Resources:
Visit
the worlds largest web site on
MIG and flux cored weld process
controls..